Imagine you have a quart-sized jar full of jelly beans. You’ve been asked to provide an accurate report of how many beans are within. Difficult, right? Now imagine you have a 50-foot-tall pile of jelly beans. How many beans do you have now? How much does that pile weigh? Would you sign a contract or pay money expecting to receive an accurate answer? Probably not.
So, how can clients trust they are receiving accurate numbers when purchasing things like rock, sand, or aggregate for landscaping, paving, or larger-scale construction projects? Similarly, how might entities such as waste or biosolids producers know how much material is at hand to treat or landfill? How can a farmer know how much manure, compost, feed, or grain they have by volume or mass? By working with companies who employ drones to collect accurate stockpile measurements. Because accuracy is important in all these scenarios — and equates to money spent or loss, regulatory compliance met, and operations conducted in response to data instead of guesswork.
Organizations who manage raw landscaping and building materials, rock and sand quarries, construction stockpiles, biosolids or composting yards may seem like unsuspecting beneficiaries when it comes to utilizing the capabilities of small, unmanned aircraft systems (sUAS). Quite the contrary. Flying a drone to accurately confirm stockpile quantities has become the most reliable, safe, and trustworthy way to forecast material production or sales, manage multiple materials across sites, retain customers, comply with regulations, and streamline data gathering and reporting.
For Accuracy in Business
Keeping an accurate inventory of the quantity, weight, and location of each material is a challenge. There may be dozens of varieties, grades or sizes of rock, gravel, or sand, for instance. Piles may spread across several properties or be relocated often to accommodate supply or demand. For these business owners, every stone or ounce of material equates to dollars won or lost. For customers of these businesses, precise numbers equate to an honest and fair return on their investment. Generating an accurate count means a win-win situation for both. Not only that — but forecasting and meeting the high demand for specific materials across a short northern construction season requires a significant logistics lift to crush and distill those materials from other material piles across several sites.
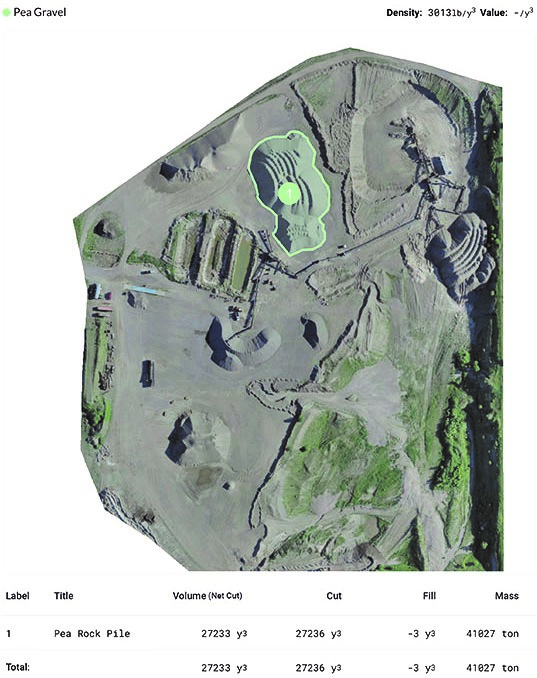
Determining the volume and mass of a pea gravel pile at Midwest Asphalt in Minnesota.
Until recently, businesses like these have relied upon calculated guesswork, equipment scales, and a combination of truck tickets to estimate what volume of crush materials might remain on property. This has generally sufficed, provided that paperwork is always thoroughly recorded, scales are routinely calibrated, and inventories are frequently conducted. Traditional land surveys have helped fill in the gaps, but are often less precise and less safe, positioning surveyors on the top of large material piles in order to attempt to collect data points.
Relying on the aforementioned methods of inventory can lead to discrepancies in purchasing and processing timelines. When does management know when to buy more source material or crush more rock to create certain types of gravel? How can they be sure that all product loads are being efficiently tracked, piled, and accounted for?
In cases like this, quantity matters just as much as quality.
Professional drone services now provide the solutions. Because accurate inventory equates to added value, drone flights are saving companies both time and money, as well as building critical customer trust when competition is more formidable than ever. In 20 minutes or less, a licensed drone pilot can fly an entire quarry or stock yard with minimal disruption to daily operations. In under 30 hours, company owners can be provided with much more accurate tonnage estimates for every pile across all quarries in their operation. Using specialized software which leverages data from the drone, a customized report for the whole quarry is generated automatically, detailing each pile’s tonnage and volume. It is so efficient, in fact, that several pits can be flown in a narrow window, synchronizing total company inventory reporting to a brief moment in time. This convenience can aid with better monitoring, ordering, and budgeting — lending a big-picture view to decisions made at the ground level.
Case Study: Midwest Asphalt Services – Twin Cities Metro, MN
Midwest Asphalt has been serving as a commercial, municipal, and residential paving company for the greater Minneapolis/St. Paul Metro since 1968. They offer a variety of construction aggregates including Class 7 Recycled Base, washed rock, washed sand, bituminous aggregates, processed topsoil, granite landscape road and more.
MSA was asked to utilize its industry leading drone technology and software to deliver automated reporting of every pile’s material, volume, and estimated tonnage for every stockpile across three active Midwest Asphalt quarries in the Twin Cities Metro area. Flights are conducted on a monthly schedule, with each pile flown the same day. The result is a simple two-page map report in PDF format that is generated in less than 24 hours. This report ensures a consistent picture of system-wide inventory. Due to the cost savings, increased safety, and reliability of this methodology, Midwest Asphalt had previously relied solely on MSA’s drone program for their inventory management, but now conducts operations with in-house pilots. MSA can also assist other firms with establishing their own program of drone operations internally as a service.
For Regulatory Compliance
Wastewater treatment plants or producers of biosolids can also find great efficiency in utilizing drones to calculate material volume and tonnage. Similar to business pursuits in the inventory and management of assets, treatment facilities can realize great efficiency and improved accuracy in measuring any waste byproduct for regulatory reporting, compliance or disposal.
Case Study: Metropolitan Council Environmental Services – Empire Wastewater Treatment Plant – Twin Cities Metro, MN
The Metropolitan Council of Minneapolis-St.Paul is the region’s policy and planning agency, providing essential services to the Twin Cities metropolitan region. The council’s Environmental Services division (MCES) is responsible for wastewater treatment for 111 cities and townships across the region — a total of 2.7 million people served.
One of these facilities is the Empire Wastewater Treatment Plant (WWTF) in Farmington, MN. Originally constructed in 1979, the plant has since doubled to meet growth and has expanded operations to improve biosolids processing. Biosolids produced at the facility are dewatered and stored on paved pads and then applied onto nearby farm fields. A construction project prevented MCES from land-applying all of the stored biosolids — resulting in a quantity that has to be disposed in a landfill. MCES required a way to estimate that tonnage of biosolids to budget for the trucking and landfilling costs.
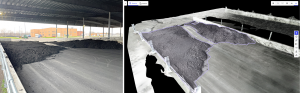
Drone photo of actual biosolids piles within a covered structure (left) and the resulting 3D volumetric models of the piles, delineated within the software for precise calculations within a complex area (right).
In November 2023, MSA completed a drone flight at the Empire WWTF with the purpose of measuring the volume of dewatered biosolids stored on paved pads — with 10 piles stored outdoors and two piles covered under a storage structure. The drone captured numerous photos of the 12 different biosolids piles, which were then downloaded into software which automates a 3-dimensional (3D) model. From this model, the volume of biosolids was determined, and the total amount of wet tonnage was calculated based on total solids concentration provided by MCES through biosolids testing.
After processing the data gathered, MSA was able to provide MCES a report within a week, showing a full set of data relative to pile identification, volume of biosolids an estimated density value, and total wet tonnage of biosolids.
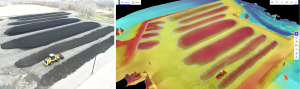
Drone photo of actual biosolids piles outdoors (left) and the resulting 3D volumetric models of the piles, visualized with an elevation gradient to assist with precisely delineating the pile edges (right).
A New Era of Asset Management
Whether a landscaping company, quarry, asphalt pit, stock yard, wastewater treatment facility or farmer, two common overarching themes prevail: accuracy matters, and time is money.
Historically, organizations have needed to dedicate a great deal of time and effort to yield accurate results. Things have changed. Thanks to advances in technology and the ability to leverage drones to streamline material inventory and management, we are able to truly work smarter, not harder — with results that directly impact the bottom line.
MSA’s Aerial Solutions team is comprised of MSA staff who serve as surveyors, engineers, planners, and GIS solutions architects to help clients and communities streamline projects. The team has been active in pursuing drone technologies and software solutions since the inception of the FAA’s expansion of commercial use drones in 2016. Licensed for commercial operations, the team assists clients with a variety of projects including asset management, topographic survey, construction observation, agricultural inspection and mapping, infrastructure analysis, 3D modeling, and construction inspection.
Connect with us, and let’s get started.